Fermentation Characteristics and Operating Instructions of Chain Plate Composting Flip Machine
Compost turner machine, NPK fertilizer manufacturing process, organic fertilizer manufacturing process, crusher, mixer, screening machine are our main products. The chain plate compost turning machine has unique advantages in the production of organic fertilizer. The following is its instructions.
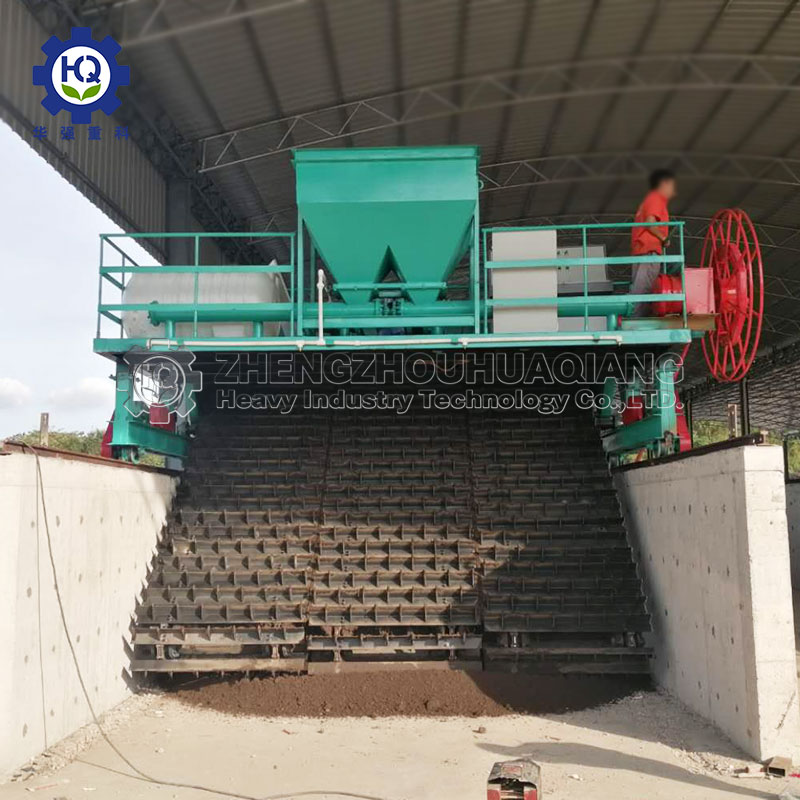
1. Chain plate compost turning machine is suitable for large-scale fermentation tanks with high and wide tanks, which can save composting workshop area and reduce civil engineering investment. The traditional trough type overturning and throwing machine is generally suitable for the height of 0. 8~1。 5 m fermentation tank, and the machine is suitable for height 1. 5~2。 It can meet the requirements of large-scale and wide tank operation. Compared with small-scale fermentation tank, the area of composting workshop can be reduced by 40 ~ 60%, and the construction cost of fermentation tank can be reduced by at least 1 / 3.
2. The chain compost turning machine adopts the supporting plate structure of chain drive and rolling support, which has small turning resistance, energy saving and is suitable for deep groove operation. The tipping support plate is equipped with flexible tension and elastic damping system to protect the transmission system and working parts for efficient operation. Through the horizontal and longitudinal shifting mechanism, the overturning parts can be operated in any position in the same fermentation tank, which improves the operation flexibility and reduces the installation capacity and power distribution requirements of the matching motor.
3. Compost turner machine is equipped with a strong and stable hydraulic lifting system to lift the overturning parts. At the beginning and end of turning, the hydraulic lifting system can be used to realize the lifting and lowering of tipping components easily through remote control or field operation, which is stable, reliable and fast.
4. The control cabinet is used to control the operation of the whole machine, and the manual control and automatic control are combined. The machine can be remotely controlled to move forward, move horizontally, flip and retreat quickly. Field operators don’t have to work at random, they can complete all operations by remote control at one end or far away of fermentation tank, which greatly improves the field environment of organic fertilizer manufacturing process.