Benefits of organic fertilizer processed by sheep manure organic fertilizer production line to land and crop production?
Benefits of organic fertilizer processed by sheep manure organic fertilizer production line to land and crop production?
1. Wide adaptability
Sheep manure organic fertilizer is suitable for sandy soil and cohesive soil. It can be applied to various crops and can increase production, quality and efficiency.
2. Protect the rhizomes of crops and provide them with comprehensive nutrition
Sheep manure organic fertilizer contains a lot of nutrients, trace elements, sugars and fats needed by plants. The CO2 released from the decomposition of sheep manure organic fertilizer can be used as a material for plant photosynthesis. Sheep manure organic fertilizer also contains 6-8% nitrogen, phosphorus, and potassium, and 50-55% organic matter, which can provide comprehensive nutrition for crops.
3. Improve soil quality and promote the reproduction of soil microorganisms
The microorganisms in sheep manure organic fertilizer multiply very quickly in the soil, leaving many thin tubes in the soil, which not only increases the permeability of the soil, but also makes the soil fluffy and soft, and nutrients and water are not easily lost, thereby increasing the soil’s water and fertilizer storage. Ability to avoid and eliminate soil compaction. The beneficial microorganisms in sheep manure organic fertilizer can also inhibit the reproduction of harmful bacteria, so that pesticides can be used less.
4. Enhance crop resistance to disease, drought, and waterlogging tolerance
Because sheep manure organic fertilizer contains vitamins and natural antibiotics. It can enhance crop resistance and reduce or prevent disease.
5. Increase crop yield
The beneficial microorganisms in sheep manure organic fertilizer use the organic matter in the soil to produce secondary metabolites, which contain a lot of growth-promoting substances.
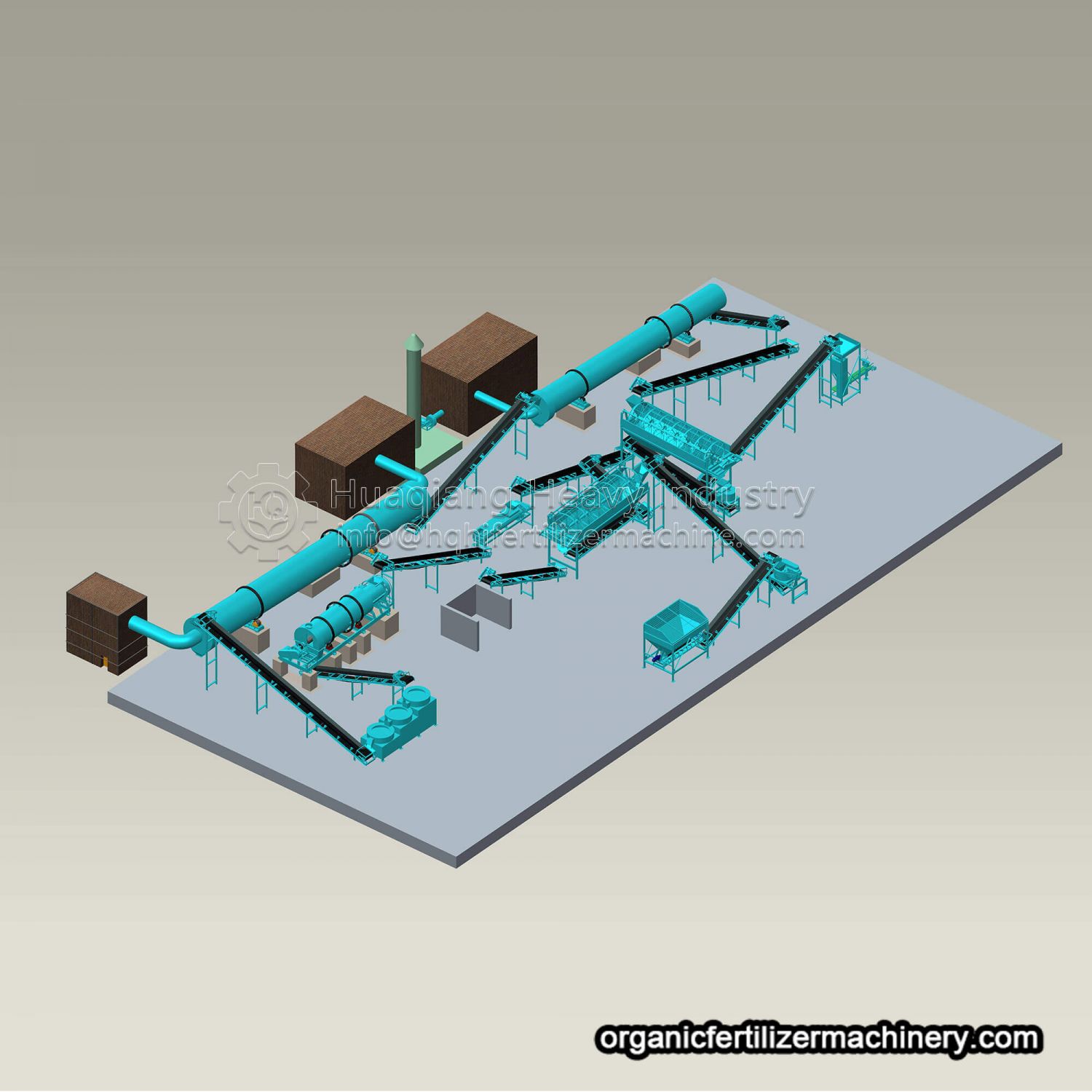
The sheep manure is pulled to the organic fertilizer production plant, and the organic fertilizer manufacturing equipment is used to make it fermented to achieve harmless treatment. After being decomposed, it is crushed, sieved, granulated and packaged into organic fertilizer. After that, organic fertilizers are classified, processed, packaged into different specifications for different types of fertilizers, such as field crops, orchard vegetable bases, landscaping, and home gardening, and then sold.