Installation and commissioning of drum granulator in npk fertilizer production line
1.Installation: After the drum fertilizer granulator machine arrives at the factory, it is installed in conjunction with the granulation process, indicating the elevation and horizontal position, and inclined installation. The general inclination is 2-5 degrees (can be adjusted by the user). The machine bracket and The transmission frame has anchor holes and can be installed on concrete.
The total thickness of the pedestal pad between the base and the foundation of the machine should not exceed 30-35㎜;
1.Adjust the height of each base with a toroidal pad to incline each base by 5 degrees;
2. The adjustment of each base is suitable for placing the cylinder on the bracket, and finally adjusting the supporting roller;
3.Install the transmission part of the granulator;
4.After making sure that the supporting roller, transmission device and cylinder are adjusted properly, start pouring cement.After 8-10 days, after the cement has set, start the no-load test run;
5. Adjustment method of body position:
a. On the full length of the left and right sides of the body, install two parallel steel wires with a wire diameter of 0.5-1㎜ and check the level of the steel wire with a level meter;
b. Put down two phase hammers tangent to the round from each round along the sides of the dryer.
c. Measure the distance between the wire and the wire sink to detect the body in a horizontal position;
d. Detect the relative vertical elevation of the highest point of the two rounded circles to check the position of the body on the vertical plane;
e. Use the method of moving electric roller to adjust the measurement of c and d, so that the body is in the correct position;
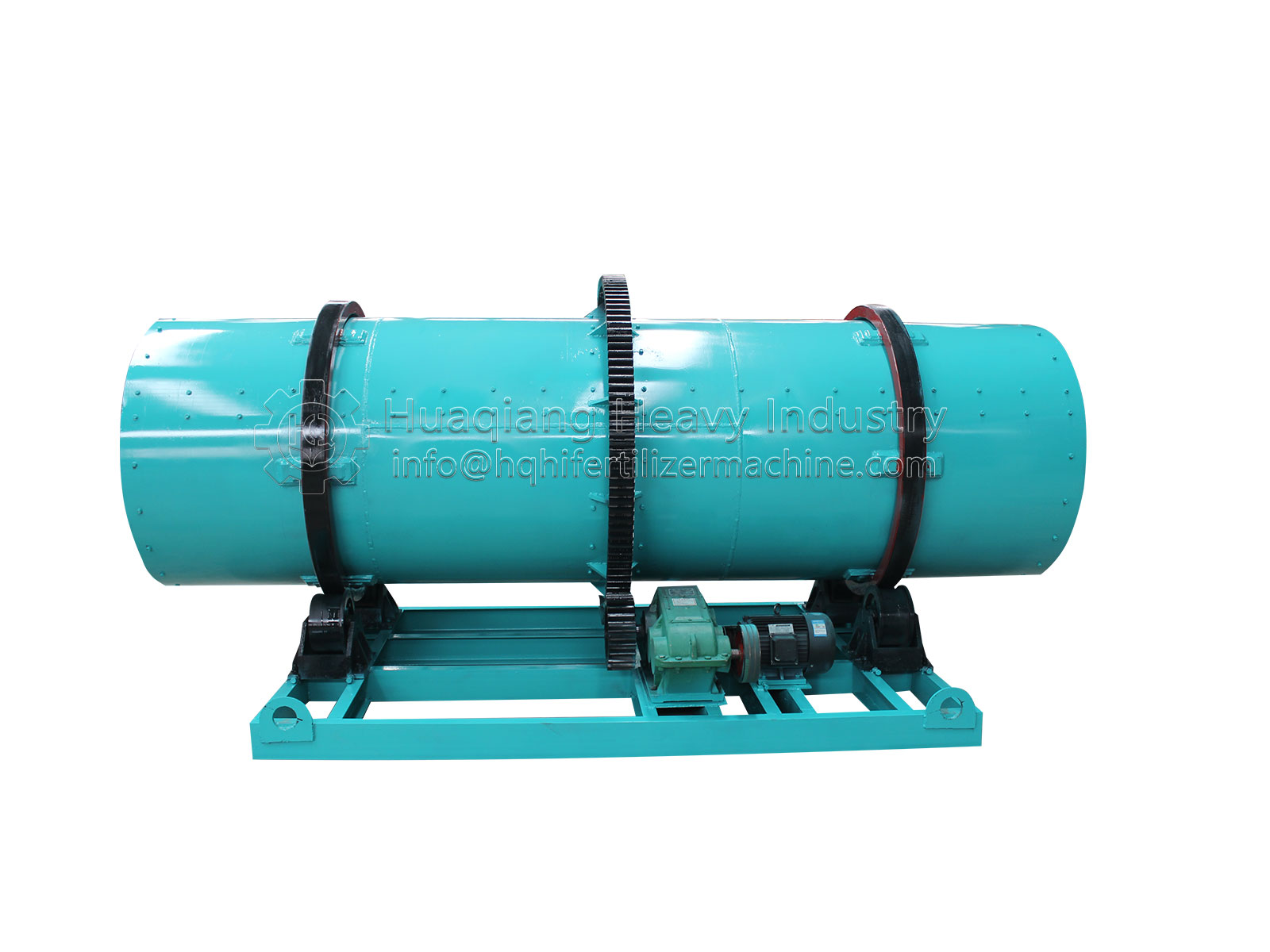
2. No load test:
a. The temperature of each bearing should rise steadily for 8 hours with no load on different ground, and the bearing temperature should not be higher than 50 ℃ at the end of the test run;
b. The noise of the gear should be uniform, and should not be high and low;
c. After the test run, observe that the bearings must not have serious wear and scratches.