What is the production process of an organic fertilizer production line?
In terms of equipment, an organic fertilizer production line requires a fermentation compost turner, fertilizer crusher, fertilizer mixer, fertilizer granulator, fertilizer dryer, fertilizer cooler, fertilizer screening machine, fertilizer packaging machine, fertilizer conveyor, and fertilizer coating machine.
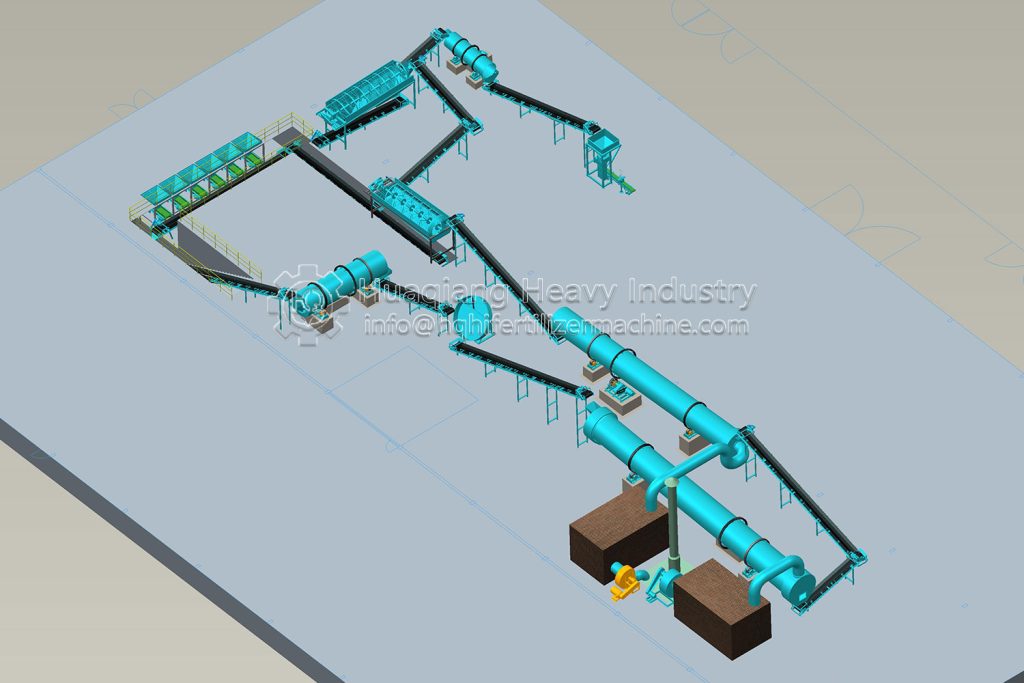
The raw materials used in organic fertilizer production vary widely, including livestock and poultry manure, municipal sewage sludge, and animal and plant residues. These raw materials are rich in organic matter, nitrogen, phosphorus, potassium, and other nutrients, providing essential nutrients for crop growth and are available at low prices.
How an organic fertilizer production line works:
Organic fertilizer processing primarily involves collecting, crushing, and mixing the raw materials. The raw materials are then mixed according to the desired formula, and the moisture content and carbon-nitrogen ratio are adjusted before the fermentation process begins.
Fermentation compost turning machines: Assist in turning the compost during the fermentation process, provide sufficient oxygen, and control the temperature to ensure uniform and thorough fermentation.
Fertilizer mixers: If the size and state of the fermented material are inconsistent, a semi-wet material grinder can be used for fine grinding.
Fertilizer Granulator: The crushed material is processed into uniformly sized organic fertilizer granules by the organic fertilizer granulator.
Fertilizer Cooler: After granulation, the organic fertilizer still contains approximately 30% moisture. To increase its strength, the granules need to be cooled for later storage and transportation.
Fertilizer Screening Machine: After granulation, a small number of unqualified granules, some too large and some too small, will be produced. The fertilizer screening machine is used to separate these granules. Oversized granules are returned to the fertilizer crusher, while undersized granules are returned to the fertilizer granulator for regranulation. Qualified granules are then sent to the automatic packaging machine.
Fertilizer Packaging Machine: The finished organic fertilizer granules are packaged by the automatic packaging machine, completing the entire process.
It should be noted that the above configuration is for a typical organic fertilizer production line and may not be suitable for all situations. In actual production applications, different manufacturers may have different requirements regarding site and raw materials, and adjustments may be required based on actual needs.