The investment cost of organic fertilizer plant mainly includes land rent, plant construction, organic fertilizer production equipment, cost of raw materials and auxiliary materials, labor cost, electricity fee, etc. Organic fertilizer production equipment: a set of npk production line: fermentation turning and throwing equipment, feeding hopper, crushing equipment, granulator, screening equipment, cooling dryer, belt conveyor, packaging equipment, etc.), granular production line, 250,000; The larger the annual production capacity, the higher the price.
Organic fertilizer granulator is one of the core equipment of organic fertilizer equipment, which directly affects the roundness, uniformity, fertilizer and water retention performance of organic fertilizer particles. Different types of granulators should use different types of granulators to directly affect the output, quality, appearance, price of the product. In the npk manufacturing process, what type of granulator is needed for the production of granular organic fertilizers. Learn about the double-roll granulator and the drum granulator today.
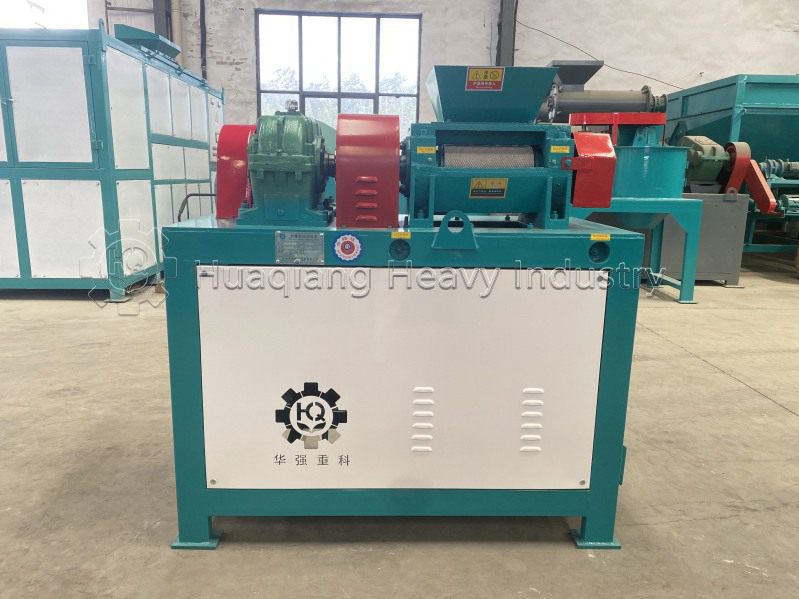
Double roller press granulator
The double roller granulator belongs to dry granulation, no drying process is required, and the granulation density is high, the fertilizer effect is good, and the organic matter content is full. Save the cost of buying dryer and cooler, no need to burn coal in the later stage, which saves a lot of money. The size of the extrusion force can be adjusted by hydraulic pressure, and the operation is flexible. It is suitable for various industries such as fertilizer, medicine, chemical industry, and feed. The design is reasonable, and it can be used together with the corresponding equipment to meet the continuous production of the production line.
Rotary drum granulator
The rotary drum granulator is a process of compound fertilizer granulation. It can also be used to produce organic fertilizer. It has high work efficiency and is lined with rubber engineering plastic material. The granulation rate is high, there is a small amount of returned material, the particle size of the returned material is small, and it can be re-granulated again, saving costs, and heating the material by steam to increase the temperature of the material, so that the moisture of the material is low after the material is formed into a ball, and the drying efficiency is improved.