What equipment is needed for a whole NPK fertilizer production line
Generally speaking, the production of organic fertilizer can be divided into four main steps: fermentation crushing granulation drying packaging. These necessary steps also have more extended procedures, such as stirring, cooling, screening and packaging.
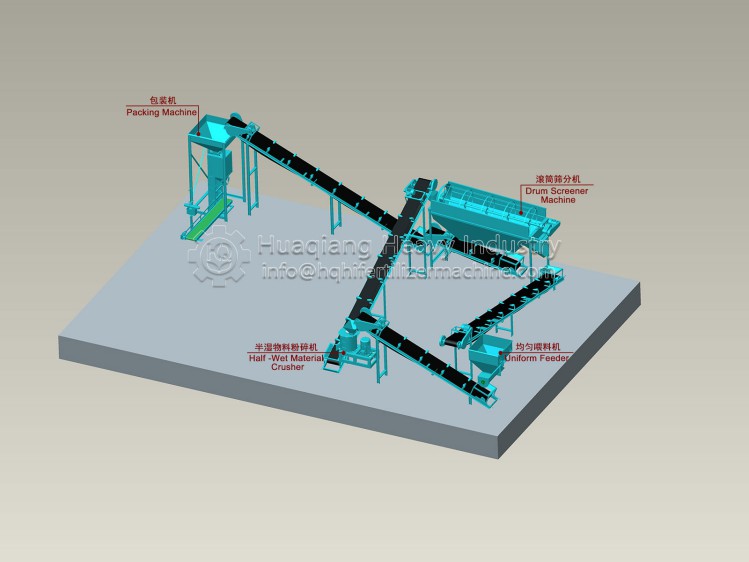
How to choose the customers of these organic fertilizer production lines often depends on the raw materials needed to make organic fertilizer. For example, in crushing, the crusher varies according to the moisture content of the raw material. Generally, semi wet materials should be used for raw materials with high water content. The pulverizer is used for crushing. If it is dry cow dung and sheep dung and other dry matter, we can use vertical crusher to crush;
In the granulation process, according to the fiber size of the raw material, we usually use the disc of the finer fiber raw material. Or drum granulator, such as chicken manure. The material of coarse fiber is flat film extruder granulator, such as cow dung, rice straw, etc.
During drying, if the budget is sufficient, we often recommend that the customer carry the cooling fertilizer production machine after drying, which is mainly to place the agglomeration caused by the overheated particles. In the later stage of granulation, there are coating and polishing processes. These are the “beauty” procedures of finished products, which make the particles more beautiful, clean and full of sales.