Anatomy of a BB Fertilizer Mixer
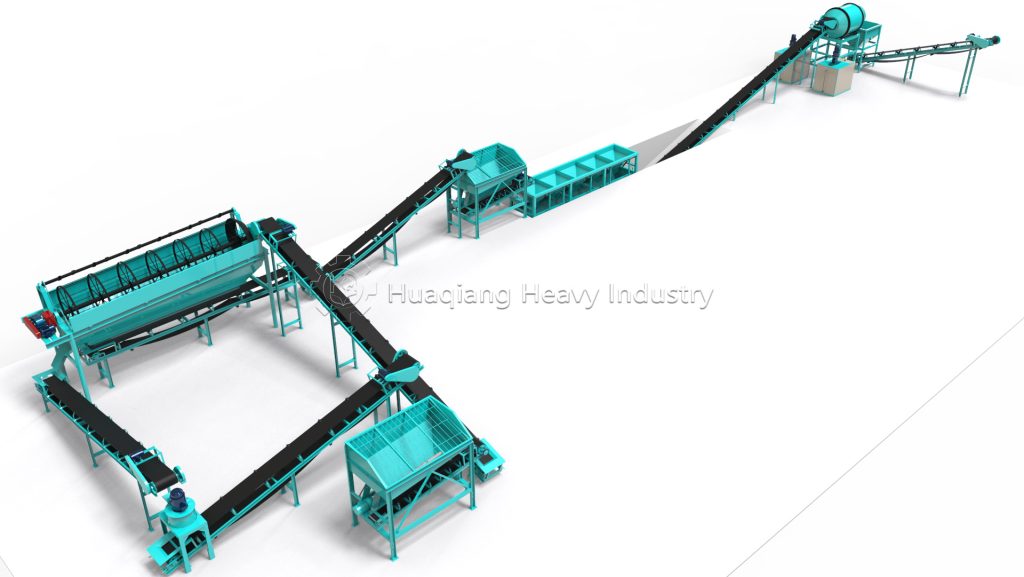
The Heart: Mixing Drum & Blades
Opening any BB fertilizer mixer reveals its mixing drum – this carefully designed enclosed space functions like a miniature ecosystem. Modern designs typically feature U-shaped or cylindrical configurations, where the streamlined structure not only looks elegant but ensures perfect three-dimensional material movement during blending.
In any bulk blending fertilizer line, the mixing device acts as the true “magician’s hand.” The high-strength alloy steel shaft is strategically fitted with various mixing elements like paddles and spiral ribbons. These hydrodynamically optimized components can uniformly blend fertilizer materials of different densities and particle sizes at 30-50 RPM, making it a cornerstone of the NPK bulk blending fertilizer line.
Power & Control Center
The mixer’s drive system resembles the human cardiovascular system:
- High-efficiency motor – IE3 energy class, 7.5-45kW power range
- Planetary gear reducer – 96% transmission efficiency, <75dB noise
- Variable frequency drive – Enables stepless speed adjustment
Modern control panels have evolved into true “smart brains.” Through 7-inch touchscreens, operators can preset 20 formula parameters while monitoring real-time data like current and temperature, ensuring each batch maintains CV values (coefficient of variation) below 5%.
Engineering Excellence in Details
Premium BB fertilizer mixers showcase professionalism in details:
- Quick-open access doors – Simplify maintenance and cleaning
- Pneumatic discharge valves – Open/close in 1 second with zero residue
- Dust-proof sealing – Triple silicone seals with <0.1% dust leakage
- Modular frame – Hot-dip galvanized for 15+ years service life
These seemingly minor designs are precisely what ensure efficient and stable operation, serving as key differentiators between ordinary equipment and industry benchmarks.