Granulation Process and Equipment Advantages of the New Type Organic Fertilizer Granulator
The new type organic fertilizer granulator utilizes the mechanical agitation force of high-speed rotation and the resulting air dynamics to continuously mix, granulate, spheroidize, and compact fine powders within the machine, achieving the desired granulation effect.
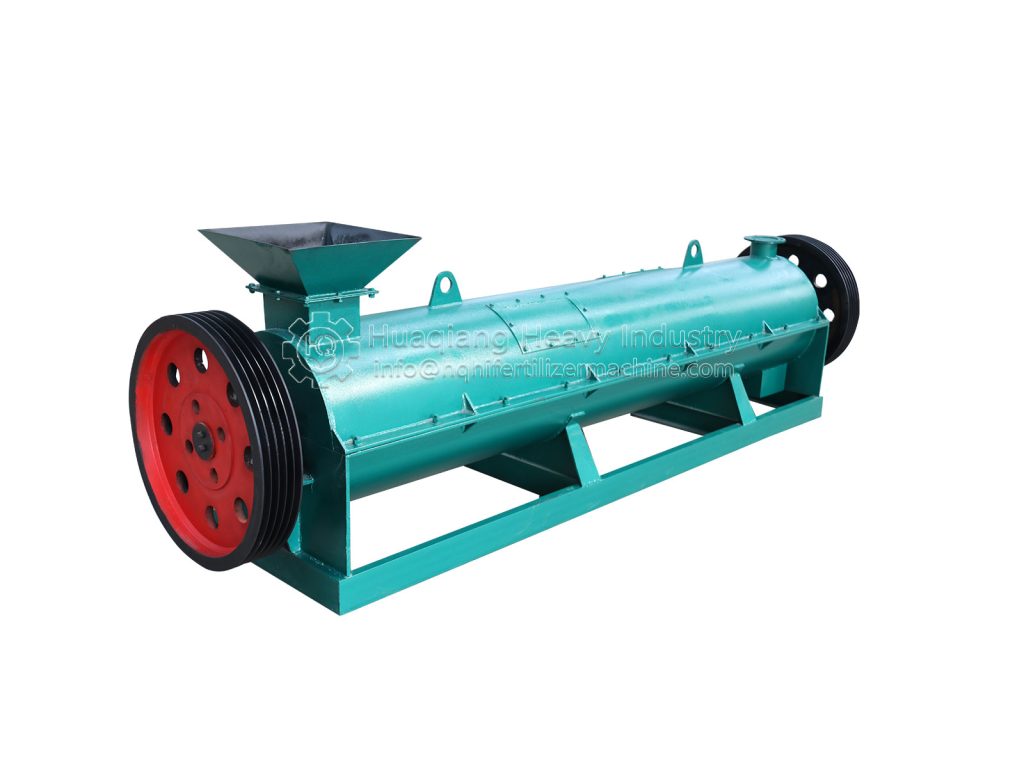
The resulting granules are spherical with a sphericity ≥0.7, a particle size generally ranging from 0.3 to 3 mm, and a granulation rate ≥80%. Particle size can be adjusted appropriately by adjusting the material mixing ratio and spindle speed. Generally, lower mixing ratios and higher spindle speeds result in smaller particles, and vice versa. This machine is suitable for granulating lightweight, fine powders. The finer the basic particles of the fine powder, the higher the sphericity and the better the particle quality. The particle size before granulation is generally required to be less than 300 mesh.
Typical applications of the new type organic fertilizer granulator include chicken manure, pig manure, cow dung, charcoal, clay, kaolin, and other materials. The new type organic fertilizer granulator boasts uniform granulation and a yield rate exceeding 97%, making it the optimal granulation equipment for organic-inorganic compound fertilizers, organic fertilizers, and bio-organic fertilizers. Due to the coarse fiber properties of the material, rotary granulators have a lower granulation rate, while agitator-type granulators cannot process materials with a nitrogen content exceeding 8% (due to sticking to the wall). This granulator overcomes the shortcomings of both, capable of producing both organic and organic-inorganic compound fertilizers with low energy consumption and high-quality granulation.
The new type organic fertilizer granulator‘s housing is welded from thickened, high-quality carbon steel plates. Ancillary equipment includes pulley assemblies, transmission components, a blower head, and a blower tail. The entire machine is sturdy and durable. The core agitator is precision-cast from a high-chromium alloy and undergoes a special heat treatment, resulting in wear resistance over three times greater than that of ordinary steel. It can withstand the high-frequency friction of fine powders for long periods of time. The main shaft and agitator blades feature a modular design and are fastened with high-strength bolts, enabling easy assembly and simple component replacement, reducing maintenance costs. Adjustable support feet on the bottom of the machine adapt to the flatness of the site, ensuring stable operation and reducing vibration-induced noise and component wear.