Working principle and equipment characteristics of disc granulator
Common organic fertilizer granulators include: npk fertilizer granulator, rotary drum granulator, disc granulator machine, new organic fertilizer granulator, new two-in-one organic fertilizer granulator, flat die granulator machine, ring die granulator, each granulator has its own production characteristics, and the price of granulator varies. Let’s learn about the disc granulator together today.
The disc granulator machine is an important part of the organic fertilizer or npk manufacturing process. Disc granulator is widely used to produce round granules of organic fertilizer and compound fertilizer. In this way, granular fertilizers are easy to transport and store. The fertilizer granulator is characterized by its wide application range and granulation rate up to 93%. It is an ideal granulator for you to produce fertilizer among many machines. Our company has various types of fertilizer granulators with different inner diameters, side heights and rotating speeds. In addition, as a disc granulator supplier, environmental disc granulators with different production capacities can meet the requirements of our customers. In short, it has the popularity and potential of granular fertilizer production enterprises in the world.
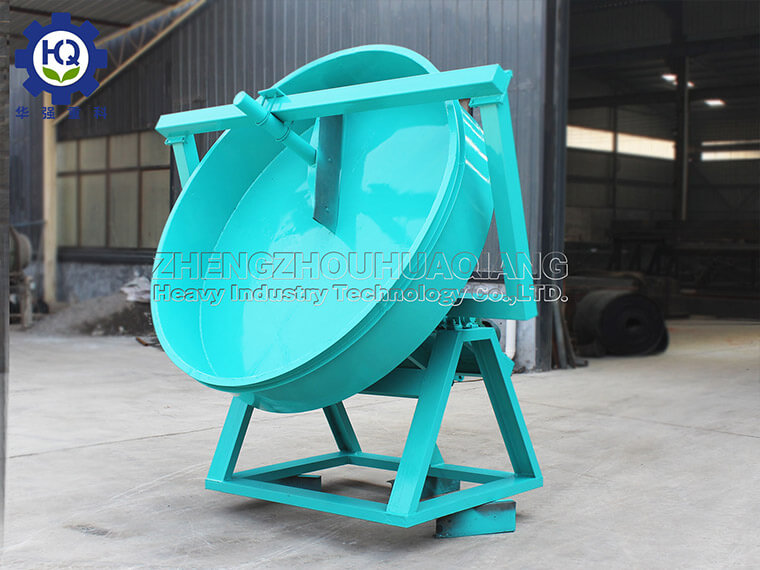
Working principle of disc granulator machine:
1. Disc
The disc is lined with high-strength fiberglass, which is corrosion-resistant and durable. The bottom of the pan is reinforced with multi-layer radiant steel plates, which is durable and never deformed. Sturdy base design, no need for anchor bolts, smooth operation. The automatic cleaning board above the sticky material improves the service life of the equipment and saves labor. The disc design ensures a high granulation rate, and the finished product rate is as high as 93%! The diameter of the disc granulator is proportional to the capacity ratio.
2. The gear of the disc granulator machine
The gear adopts high-frequency quenching, which doubles the service life.
3. Motor and reducer
These parts are powerful and reliable with a long service life.
4. Transmission belt
The motor and reducer are driven by flexible belts to ensure smooth starting, increase the service life of the equipment, and reduce the compactness.