Current Status and Development Trends of the Rotary Drum Granulator Market
As a key piece of equipment for powder granulation, the current market for rotary drum granulators exhibits distinct characteristics and clear trends.
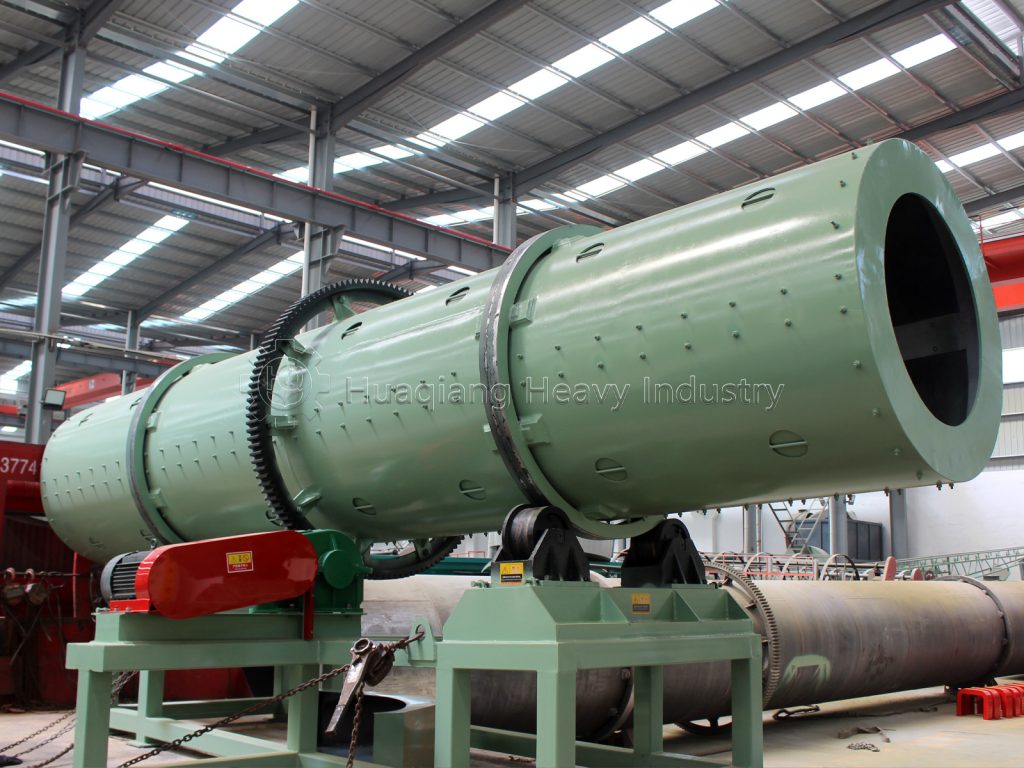
Currently, market demand for rotary drum granulators is extremely strong. In the agricultural sector, with growing interest in green and environmentally friendly fertilizers, the production of organic and compound fertilizers is expanding, significantly driving demand for drum granulators. Many organic and compound fertilizer manufacturers are investing in advanced rotary drum granulators to improve production efficiency and ensure product quality. In addition to agriculture, industries such as chemicals and feed are also increasing their investment in drum granulators due to demand for granular products.
Market competition is becoming increasingly fierce. The influx of manufacturers has led to a complex product range and varying quality. Large companies dominate the market, leveraging their strengths in technological research and development, quality control, and after-sales service networks. Smaller companies rely on low prices to compete, but lag significantly behind in quality and innovation.
Technically, high-end equipment is becoming the mainstream. Models with automated control, intelligent monitoring, and high-efficiency energy-saving features are increasingly popular. They improve production efficiency and product quality while reducing labor and energy costs, meeting the demands of intelligent and green production.
Future development directions are clear: First,intelligent upgrades: equipment will enhance self-diagnosis and automatic adjustment capabilities, enabling parameter adaptation and unmanned production. Second,deepening energy conservation and environmental protection efforts: adopting advanced technologies and designs to reduce energy consumption and emissions, meeting stringent environmental requirements. Third,specialized segmentation: developing customized products for different industries, raw materials, and needs to meet individual market demands.
In short, the rotary drum granulator market presents both opportunities and challenges. Companies must focus on technological innovation, quality improvement, and service optimization to remain competitive.