How to Choose the Right Double Roller Press Granulator for Farms
Due to its unique advantages, double-roller press granulators have become essential equipment for farms to process manure and produce organic fertilizer. When selecting a granulator, you need to consider multiple factors to ensure it meets your production needs.
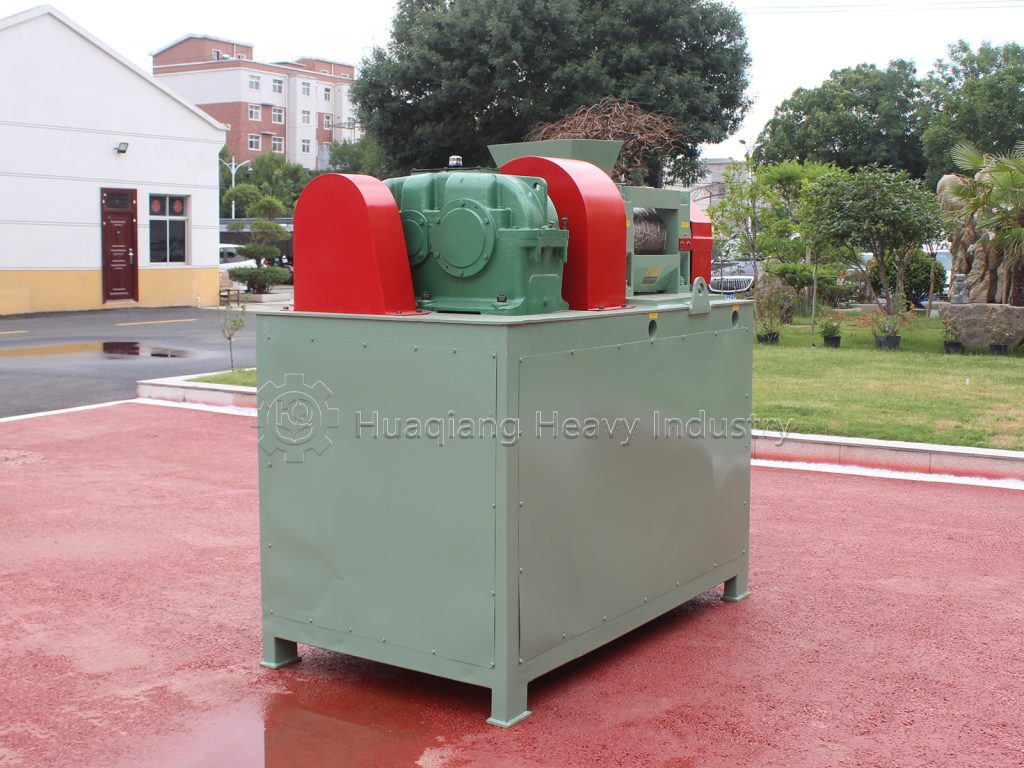
First, you need to determine your production scale. Small and medium-sized farms have limited daily manure processing capacity, so choosing a small machine with an hourly capacity of 1-3 tons can meet daily granulation needs while avoiding idle equipment. Large-scale farms require a machine with an hourly capacity of 5 tons or more and strong continuous operation capabilities to ensure timely manure processing and stable fertilizer output.
Second, consider the characteristics of the raw materials. Farms primarily use livestock and poultry manure as their raw material, which is high in moisture and contains impurities such as crude fiber. Therefore, the equipment needs to have strong anti-clogging capabilities, and the roller surface should be made of a non-slip and wear-resistant material to prevent slippage and affect granulation efficiency.
Supporting facilities should be planned simultaneously. It’s recommended to use pre-treatment equipment such as dewatering machines and crushers to control the moisture content of raw materials within an appropriate range, and to configure screening devices to grade finished particles to improve fertilizer quality. Furthermore, consider equipment energy consumption, prioritizing energy-efficient models to reduce operating costs.
A balance should be struck between price and after-sales service. Avoid blindly pursuing low-priced equipment, as its materials and workmanship may be defective and increase maintenance costs. Choose a manufacturer that can provide installation and commissioning, operator training, and rapid fault response to ensure stable operation after the equipment is commissioned and minimize losses caused by downtime.
A comprehensive assessment of production scale, raw material characteristics, equipment quality, supporting capabilities, and after-sales service is crucial to selecting a double-roller press granulator suitable for your farm, ensuring efficient resource utilization of manure.