NPK compound fertilizer production lines meet diverse needs
The diversified development of modern agriculture has created diverse fertilizer demands. With its strong adaptability and flexibility, NPK compound fertilizer production lines perfectly meet these diverse needs, providing comprehensive services for the vigorous development of modern agriculture.
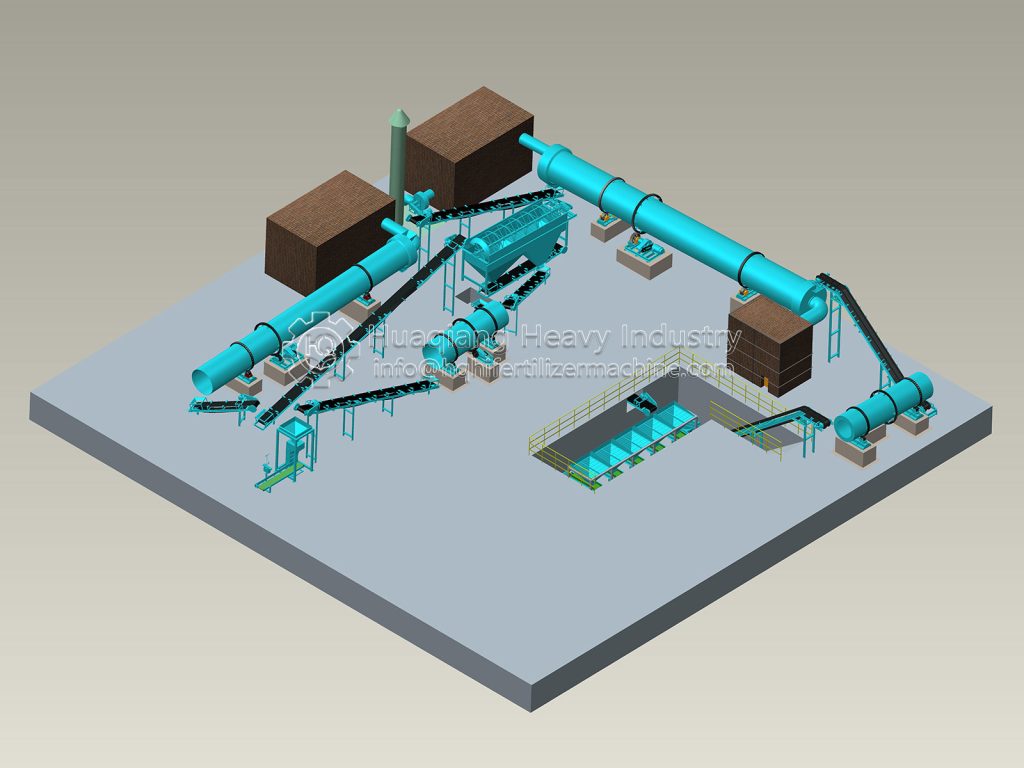
Different crops have vastly different nutrient requirements during growth. NPK compound fertilizer production lines can customize fertilizer formulas based on the characteristics of each crop. For grain crops like wheat and rice, the line can produce fertilizers with appropriate nitrogen, phosphorus, and potassium content and ratios, improving yield and quality. For cash crops like cotton and tobacco, the line can adjust the formula to increase the content of certain trace elements, thereby enhancing the crop’s resilience and economic value.
Soil conditions are also a significant factor influencing crop growth. In acidic soils, NPK compound fertilizer production lines can produce slightly alkaline fertilizers to neutralize soil acidity. In areas with poor soils, the line can produce fertilizers with high nutrient content and long-lasting effects, rapidly improving soil fertility. Through this customized fertilizer production, NPK compound fertilizer production lines can help farmers overcome the planting challenges presented by varying soil conditions. With increasing attention to food safety and environmental protection, the demand for green and environmentally friendly fertilizers is growing. The NPK compound fertilizer production line actively responds to this trend, utilizing environmentally friendly raw materials and clean production processes to produce low-pollution, low-residue fertilizers. These fertilizers not only help reduce agricultural non-point source pollution and protect the ecological environment, but also produce agricultural products that meet green and organic standards, satisfying consumer demand for healthy food.
The NPK compound fertilizer production line will continue to keep pace with agricultural development, continuously innovating and improving, and providing a stronger foundation for the sustainable development of modern agriculture.